Revolutionizing Distribution Network Optimization and Warehouse Operations
The supply chain industry is undergoing an unprecedented transformation, driven by rapid technological advances and evolving customer expectations. As a subject matter expert and founder of a supply chain consulting firm in business for more than two decades supporting Fortune 500 and mid-market companies worldwide, I can confidently say that the future of supply chain management will hinge on embracing technology to optimize distribution networks, warehouse processes, and operations. This article explores how technology will reshape supply chain strategies, focusing on distribution network optimization, engineered warehouse operations, and the balance between service level, capital costs, labor, and operational efficiency.
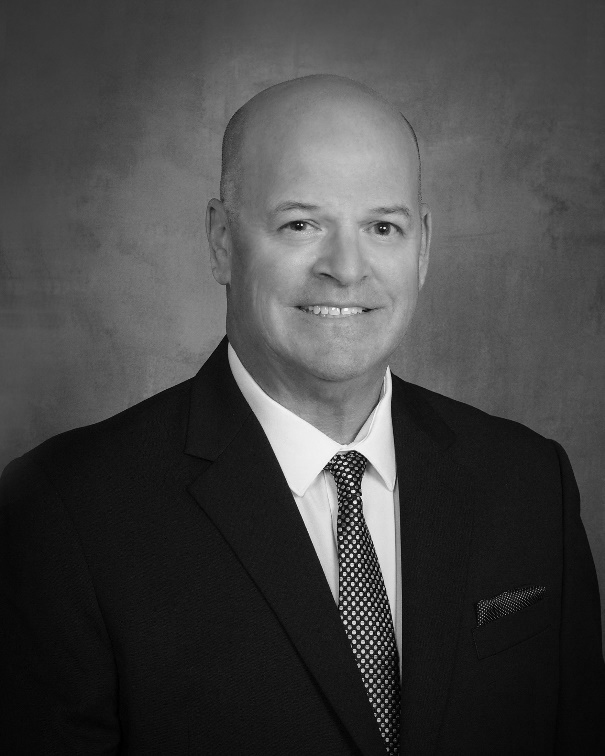
Technology-Driven Distribution Network Optimization
Distribution Network Optimization (DNO) is a critical supply chain element, especially as companies strive to improve customer service, reduce lead times, and control costs. Technological advancements in data analytics, machine learning, and predictive modeling will significantly enhance DNO by providing greater accuracy and agility. Key considerations for future DNO include:
Determining the Optimal Number and Location of Distribution Centers (DCs)
A primary decision in distribution network design is the number and geographic placement of DCs. Traditionally, companies have relied on balancing proximity to customers and operational costs. However, with technological tools like advanced geospatial analysis and AI-driven scenario modeling, companies can now evaluate potential locations with greater precision, factoring in variables such as regional demand fluctuations, logistics costs, and geopolitical risk.
Predictive Analytics for Demand Forecasting: Predictive algorithms will enable firms to forecast demand patterns more accurately, identifying locations with high growth potential and minimizing unneeded capital expenditure in under-utilized regions.
Resiliency through Diversification: Technology will enable companies to diversify their networks based on risk management. AI tools can predict how factors such as trade disruptions, regulatory changes, or climate events will affect each location, allowing firms to create a resilient network with multiple supply routes and backup facilities.
Capacity and Throughput Requirements
As consumer expectations evolve towards faster delivery, companies must ensure their DCs can handle fluctuating demand levels. Capacity planning, driven by AI and machine learning models, will help firms design facilities with flexibility in mind, accommodating peak seasons without excessive fixed overhead costs. This planning includes throughput requirements, which determine the speed and volume at which inventory moves through each DC.
Dynamic Modeling for Demand Peaks: Future DCs will increasingly rely on dynamic modeling, using real-time data to adjust inventory and staffing in response to short-term demand peaks.
Throughput Optimization with Simulation Software: Simulation tools will become essential for identifying bottlenecks in the movement of goods, from unloading to staging to outbound transportation. This approach will enable better staffing decisions, optimized equipment use, and improved space utilization.
SKU and Inventory Depth Optimization
Choosing the right SKUs and maintaining optimal inventory depth at each location are crucial for balancing service levels and inventory costs. Using technology, companies can assess SKU demand profiles across different regions, ensuring each DC stocks products that align with local customer preferences and demand patterns.
AI-driven SKU Segmentation: Advanced analytics can segment SKUs based on historical data and customer profiles, enabling firms to determine which items should be stocked at specific DCs and which can be held centrally or manufactured on demand.
Inventory Optimization Algorithms: Algorithms that consider lead times, customer service requirements, and storage costs will help determine optimal inventory depth. These systems automatically adjust inventory levels as demand patterns change, ensuring a balance between availability and carrying costs.
Customer Service Alignment with DC Allocation
Customer proximity and service expectations increasingly drive the allocation of customer accounts to specific DCs. With technology, companies can employ optimization algorithms that balance delivery speed, cost, and customer satisfaction across multiple DCs.
Customer Prioritization Models: These models prioritize high-value customers or those with stringent service requirements, ensuring they are served from the closest, best-equipped facility.
Service Level Agreements (SLAs) and Network Optimization: Companies will implement SLA-driven network designs, ensuring that DCs are aligned with service standards. Technology can analyze customer-specific SLAs to allocate resources where they’re most needed.
Optimally Engineered Warehouse Operations
In the future, warehouse operations within the four walls of a DC will be driven by technological advancements, from the layout of systems and processes to the blend of infrastructure, labor, and automation. Technology will enable companies to engineer warehouses for optimal efficiency, scalability, and adaptability.
Process Optimization Through Technology
Process optimization within the warehouse will be foundational to achieving operational excellence. Key to this will be systems like Warehouse Management Systems (WMS), AI-driven analytics, and automation platforms that streamline workflows, reduce human error, and enhance productivity.
Integrated WMS with Real-Time Analytics: Next-generation WMS will integrate seamlessly with data analytics platforms, providing real-time visibility into inventory and order statuses. This data will be invaluable for reducing lead times, optimizing storage allocation, and managing labor effectively.
Automated Task Allocation: AI-powered systems will automate task allocation to warehouse associates, ensuring tasks are assigned based on skills, proximity, and workload. This will reduce idle time and maximize productivity.
Balancing Infrastructure, Labor, and Automation
Future warehouse operations will require a strategic combination of infrastructure investment, labor, and automation to maintain operational flexibility while managing costs.
Flexible Infrastructure Design: As demand fluctuates, warehouses need the flexibility to reconfigure spaces for different functions (e.g., from storage to order picking). Modular racking systems and multi-purpose layouts will support this need.
Labor Augmented by Robotics: Robotics will augment human labor, especially for repetitive tasks like picking, packing, and sorting. Collaborative robots (cobots) will allow human workers to focus on more complex tasks, reducing fatigue and improving efficiency.
Hybrid Automation Models: The future warehouse will incorporate hybrid automation, combining manual processes with mechanized and robotic systems. This approach ensures scalability and flexibility while reducing dependency on labor for repetitive tasks.
Capital and Operational Cost Considerations
Adopting new technology is managing capital and recurring costs while balancing capacity, throughput, scalability, and risk. Different levels of automation offer unique cost-benefit profiles, which firms must carefully consider.
Capital Costs
The upfront investment in warehouse infrastructure and technology varies widely depending on the level of automation:
Manual Operations: Manual setups are the most capital-efficient but may lack the throughput and scalability needed for high-demand environments.
Mechanized Systems: Mechanized systems, such as conveyor belts and automated storage, are moderately expensive and improve efficiency without full automation.
Automated and Robotic Systems: Fully automated systems have high capital costs but maximize throughput and reduce long-term labor expenses, making them ideal for high-demand DCs with stable demand.
Recurring Costs (Labor)
Labor costs are a significant component of ongoing expenses. Depending on automation levels, warehouses can manage labor costs effectively.
Manual Operations: These involve a high reliance on labor and recurring costs that vary based on workload. These systems also introduce potential variability in productivity.
Mechanized Operations: These setups require fewer manual laborers and reduce costs while maintaining flexibility.
Robotic Systems: Robotics significantly reduce recurring labor costs by automating repetitive tasks, offering long-term savings and consistency in performance.
Capacity, Throughput, Flexibility, and Scalability
Warehouse technology directly impacts capacity and throughput. Fully automated warehouses can handle large volumes with high accuracy, while hybrid models offer flexibility to adapt to changing demand patterns.
Capacity: Automated systems typically offer higher capacity by optimizing space utilization, while manual systems require more space for the same volume of goods.
Throughput: Robotics and automated systems provide higher throughput, handling more items per hour than manual operations.
Flexibility and Scalability: Hybrid models combining labor and automation provide the best balance, allowing for adjustments in labor and equipment as demand fluctuates.
Risk Management in Technology-Driven Warehouses
Each type of operation involves risk trade-offs:
Manual Operations: High risk due to dependency on labor availability and quality, but more resilient to system failures.
Mechanized Operations: Moderately resilient with lower dependency on labor but still susceptible to mechanical issues and capacity constraints.
Automated and Robotic Systems: These systems are more capital-intensive and potentially vulnerable to technical disruptions. However, they reduce risk related to labor shortages and offer consistent performance under stable demand.
Achieving a Technological Edge in Supply Chain Management
Technology is not a one-size-fits-all solution; it requires a thoughtful approach to integrate with organizational goals, service standards, and budget constraints. To succeed in the coming years, companies must embrace a holistic strategy that optimizes the entire supply chain network—from distribution center placement and SKU management to warehouse operations and the balance of labor and automation.
Invest in Predictive Analytics and AI: Use these tools to make smarter decisions about DC placement, inventory levels, and customer allocation, enhancing responsiveness to market demands.
Adopt Scalable Warehouse Technology: Choose flexible, scalable systems that allow for quick adjustments to capacity, throughput, and labor needs.
Balance CapEx and OpEx: Ensure that capital investments in technology align with long-term operational cost reductions, particularly in labor-intensive areas.
Manage Risk Strategically: Employ technology to improve resiliency against labor shortages, demand surges, and logistical disruptions.
Seek Assistance from Outside Subject Matter Experts: (SMEs) such as OPSdesign Consulting to fill gaps in internal horsepower and expertise, freeing your internal teams to run the enterprise.
As companies evolve their supply chains in the coming years, those that successfully leverage technology for distribution network optimization and warehouse automation will be best positioned to thrive in a rapidly changing market. By investing in the right tools and strategies, firms can create robust, efficient, and scalable supply chains that meet the demands of tomorrow’s global marketplace.